Integrate Inspections at the core of your Quality Ecosystem
Optimise Quality Inspections, preventing defects through Quality Assurance. Streamline your process, ensuring defects are addressed at the source for swift corrective action. Our Solution goes beyond inspection, offering a configurable Quality Management solution with user-friendly dashboards, enhancing operational efficiency and ongoing quality assurance. ATS Inspect will talk directly to your PLM/ERP/MES/etc. providing real-time alignment.
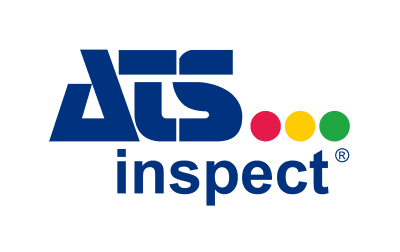
ATS Inspect, the Straightforward Quality Inspection from ATS Global
Achieve Total Quality Management with ATS Inspect,
while integrating Inspections at the core of your Quality ecosystem.
Straightforward
Quality Inspection from ATS
Connectivity
Enables seamless connectedness so you can choose to start simple or integrate with more automated systems in your ecosystem
Control
Designed to help humans take control by solving the root cause of the problem, enabling a clear view of what’s going on
Usability
Makes inspection data usable by all, enabling data lead decision making, opening the door to experts from all areas to be involved
Efficiency
Helps operations run smoother by eliminating recurring defects, only showing what you want to see for ongoing assurance
Compliance
Manages your quality standards risk, so you can achieve full product governance and have support from our experts
Eliminate Paper Checklists
You hate them, we hate them, so let’s get rid of them. No more time lost to transcription, and reports using old data. Just real-time awesomeness.
Improve Right First Time
Each defect found costs time and money so we give you the tools to find the root cause of every issue to prevent it occurring again, raising your Right First Time.
Eliminate Product Recalls
A gating system, aided by a guided inspection, ensures that every product leaves the plant exactly as your customer expects.
Capture All Defects
If you don’t have the full picture you can’t respond effectively, so we make sure you can identify every defect allowing you to make knowledge-based decisions.
Drive Continuous Improvements
Our quality inspection software brings your quality and process data together to drive cross-plant improvements.
Reduce the Cost of Poor Quality
Actionable product quality analysis enables you to achieve Best In Class rework and scrap costs while simultaneously pushing up product quality.
Got a question? Get in touch.
Success Stories